首先,可编程逻辑控制器(PLC)是工业自动化的的“大脑”。它本质上是一台工业级计算机,负责执行设备级的控制功能。PLC最初是为了替代继电器控制系统而设计的,通过减少硬件数量和简化重新配置过程,显著降低了成本。大多数PLC采用梯形逻辑编程,模仿传统的继电器 电器控制逻辑,使得编程更为直观。PLC广泛应用于各类自动化过程,从灯光控制到执行器操作,但其主要功能仍限于逻辑位操作,高级通信和数据共享则非其强项。
随着技术发展,可编程自动化控制器(PAC)应运而生。PAC相较于PLC,具备更强的处理能力和更多内存,能够执行更为复杂的任务,如PID控制、通信、SCADA系统管理等。PAC特别适合运动控制应用,其多处理器架构和高速背板设计,使其在数据采集和处理方面表现卓越。
远程终端单元(RTU)则是另一重要组件,常作为大型控制系统的一部分,尤其在DCS和SCADA系统中扮演关键角色。RTU负责监控和控制设备的各个子单元,如传感器、阀门等。现代RTU通常具备可编程逻辑功能,并通过以太网等通信手段与主控制系统连接。
分布式控制系统(DCS)则着眼于全局,用于同时控制和监控多个系统。DCS内置冗余设计,以降低故障风险,适用于全厂范围的监控和控制。DCS并非单一产品,而是一整套集成解决方案,涵盖从现场I/O到控制层和软件层。
监控与数据采集系统(SCADA)则侧重于设备和流程的实时监控和控制。SCADA系统通常包含人机界面(HMI),辅助操作员做出决策。其工作原理是通过收集各系统数据,集中处理或展示,以便操作员及时调整。
随着技术不断融合,各组件间的界限日益模糊。了解并适应这些变化,对于控制工程师而言至关重要。不仅要熟悉现有设备,更要关注未来趋势,以便更好地应对工业自动化的挑战。
现代控制系统是各种组件的共同努力,每个组件都有自己的工作要完成,协调工作为工厂或工业系统提供无缝控制。尽管组件的种类必然会随着时间的推移而发生变化,但工业自动化的当前快照揭示了一些重量级的关键参与者。
可编程逻辑控制器PLC
PLC 是可编程逻辑控制器最常见的缩写。它们是许多不同工业流程的“大脑”,本质上是工业级计算机,用于在设备级别执行控制功能。
PLC 最初的发明是为了取代继电器组作为工业自动化的控制系统,通过减少所需的硬件数量,并且无需在需要更改时对每个继电器进行物理重新接线,从而节省了继电器控制的大量成本。控制系统。这是可能的,因为 PLC 可以像任何现代计算机一样简单地重新编程。
梯形图逻辑看起来类似于传统的继电器控制图
大多数 PLC 使用某种形式的梯形逻辑进行编程,模仿物理继电器控制系统逻辑。该程序通常被称为梯形逻辑,看起来像一个由继电器和其他电气元件组成的梯子,“梯级”放置在电源之间,在侧面表示。这一切都可以在计算机上或有时(特别是在较旧的系统中)在专用界面上以数字方式显示和重新编程。
PLC 可用于许多不同的自动化过程,控制从灯光到执行器和其他控制组件的一切。但PLC,但从形式上的定义来说,只执行逻辑位操作,它本来并不处理高级通信和与上层和下层网络的数据共享。当这些功能开始出现时,这些设备的新名称开始形成。
PAC
PAC 代表可编程自动化控制器,可以被认为是具有更多功能和更高处理能力的“先进”PLC。PLC 的功能相当简单,而 PAC 通常比标准的简单 PLC 可以访问更多的内存和更高的处理能力。
它们通常用于执行涉及 PID 控制、通信、SCADA、数据记录以及其他传统上超出基本 PLC 范围的任务。
PLC 通常(或过去)功能不够强大,无法用于运动控制应用,因此 PAC 成为此类自动化控制的理想控制单元。PAC 具有一个优势,因为它们是用多个处理器芯片构建的,因此可以一次执行多个操作。此外,它们通常包含高带宽背板,使它们能够快速采集数据,从而实现更快的数据控制和高效处理。
尽管现在大多数公司实际上都在生产 PAC,但我们几乎仍然将它们称为 PLC,因为它们仍然完成逻辑控制任务,并且我们熟悉这个概念。因此,对于 PAC 是否仍被称为 PLC 几乎没有争论或争论。
顺便说一句,IPC(工业 PC)的概念正在取得长足进步,有可能成为控制系统处理器选择的下一代发展,因此本文的未来修订版可能会包括新技术!
远程终端设备RTU
远程终端单元( RTU) 是与较大控制单元分开的控制设备,通常作为较大系统的一部分。在许多情况下,它们是 DCS 或 SCADA 系统的一部分,并包含 SCADA 用于监控的一些单独组件。RTU 通常控制或监视设备的各个子单元,例如传感器、阀门、风扇和执行器。
RTU 随着时间的推移而不断发展,通常能够执行可编程逻辑,类似于现代 PLC。将信息转发回主控制系统的方法有多种,但大多数现代 RTU 使用以太网或某种类似的通信形式。事实上,Modbus RTU 是有史以来最流行的网络协议之一,其设计目的只是为了与这些设备连接。
RTU 通常是 SCADA 系统的一部分,可用于控制阀门等单个组件。上图是施耐德(左)和霍尼韦尔(右)的 RTU 示例
RTU 通常由一些通用组件组成,这些组件协同工作以构成一个成功的独立控制单元。它们通常包含某种基本 CPU 来分析输入,然后为系统做出决策或将信息转发为输出。它们还包含某种形式的本地或远程 I/O 接口,以从其操作中获取信息,以便更好地了解其所监督设备的状态。
简而言之,RTU就像一个非常基本的PLC,用于控制一些外部的、隔离的I/O设备或网络,形成更大级别的控制系统的一部分。
分布式控制系统DCS
DCS(分布式控制系统)是用于同时控制和监控多个系统的高级系统。它们通常内置一定程度的冗余,以帮助降低 DCS 发生故障时停机的风险。它们用于监控一系列系统(通常是全厂范围的),并监控信息以跟踪过程数据点并控制输出。这样可以在必要时在他们正在监控的一系列系统中更轻松地进行修改。
DCS 不是您可以购买的单一产品(如 PLC 或 RTU),而是一整套工厂级产品,从现场级 I/O 到控制器,一直到生产软件,监控和调度。
一般来说,大多数 DCS 都由同类品牌的电子控制组件组成,因此这些组件都可以轻松地相互通信。例如,新系统使用所有同一个品牌的 PLC、I/O 网络和软件来确保所有设备兼容并能够与 DCS 通信是有意义的。传统设备可以拼凑起来以接受 DCS,但这通常比从头开始设计更加复杂和昂贵。
监控与数据采集系统SCADA
监控和数据采集(SCADA)这个术语用于描述许多不同制造过程中使用的一种设备监控和控制系统。这些系统通常用于对许多系统的硬件和软件进行有效控制,以帮助提高整个工厂(或全球)流程的效率。
SCADA 系统通常包含 HMI(人机界面)作为其基础设施的一部分,用于帮助控制室的操作员做出有关系统状态的决策,并在设备状态更新时在必要时进行更改。
SCADA 系统通常是工厂控制室的中心
SCADA 的工作原理是监控工厂内的许多不同系统并将它们转发到中央位置。数据要么在 SCADA 编程中自动监控和处理,要么显示在监视器上,然后操作员可以做出正确的决策并通过 HMI 对系统进行更改。这种类型的控制系统对于需要许多不同流程才能成功协同工作的操作非常有用。
一个很好的 SCADA 示例可能是在大型过程工厂中,其中产品从一个位置移动到另一个位置,并沿途改变状态。例如,散装水泥厂需要在高温下蒸煮原材料,操作员必须在产品流经工厂时监控温度和产品的化学成分。如果产品在任何时候不符合规格,操作员可以进行适当的更改以使其恢复到规格。
控制行话
随着技术的进步,各种组件之间的界限变得模糊。一些设备已过时,而另一些设备则不断发展并与单独的设备相结合,以创建单一的、更具成本效益的解决方案。
花时间记住正式定义并不重要,因为它们肯定会发生变化,但一定要了解运行您自己工厂的设备并对未来趋势保持开放态度,并准备好了解新技术如何使您成为更有效的控制工程师。
本站声明:网站内容来源于网络,如有侵权,请联系我们,我们将及时处理。
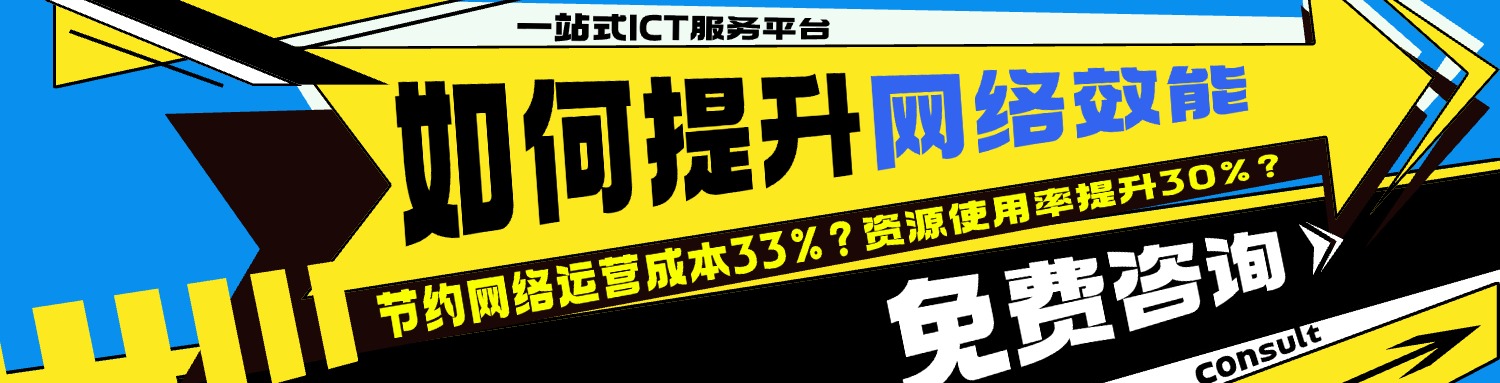